There are many different types of steel in use today, the most common of which by far is carbon steel. And clean carbon steel is black. Not grey. Not silver. Not blue. Not shiny. Black. Most people think steel is “grey”! Here’s why…
Steel is not a metal on the periodic table like gold, silver, or nickel. But it is an alloy made mostly of iron (around 95%), which is why it is naturally black (think of wrought iron). And the remaining 5% is a mixture of carbon, nickel, silicon, and/or other elements that affect its hardness, malleability, and other properties. See Figure 1 for steel products in their natural colour.
As awesome as steel is, when exposed to the elements and road maintenance chemicals, it tends to corrode (rust), which is why there are several different corrosion-resistant treatments for steel, such as paints, epoxies, and other coatings. The most common treatment for everyday outdoor steel is something called hot-dipped galvanizing. This treatment coats the steel in pure zinc, which makes it shiny or grey and highly corrosion-resistant.
Most of the steel you see on the streets and highways is hot-dipped galvanized (see Figures 2 and 3).
What makes the hot-dipped galvanizing process better than paint is that paint is a coating applied to the surface of the steel. Although this provides some level of protection, it can be chipped, exposing the steel to the elements and allowing rust to develop, and once it starts, it doesn’t stop. Galvanizing, on the other hand, embeds the zinc into the steel. The process involves dipping the steel product into a bath of molten zinc, coating the steel with zinc, which is highly corrosion-resistant. It also creates a layer of steel-zinc alloy embedded into the surface of the steel — imagine the steel absorbing the corrosion resistant zinc into itself. This is called galvanizing. Corrosion protection and zinc galvanizing are sciences unto themselves, so let’s just focus on how the process works.
Welcome to AZZ Galvanizing’s facility in Acton, Ontario. AZZ is the largest galvanizing company in North America with facilities across Canada and the U.S. They process tens of thousands of tons of steel every year in this local facility alone. See Figure 4.
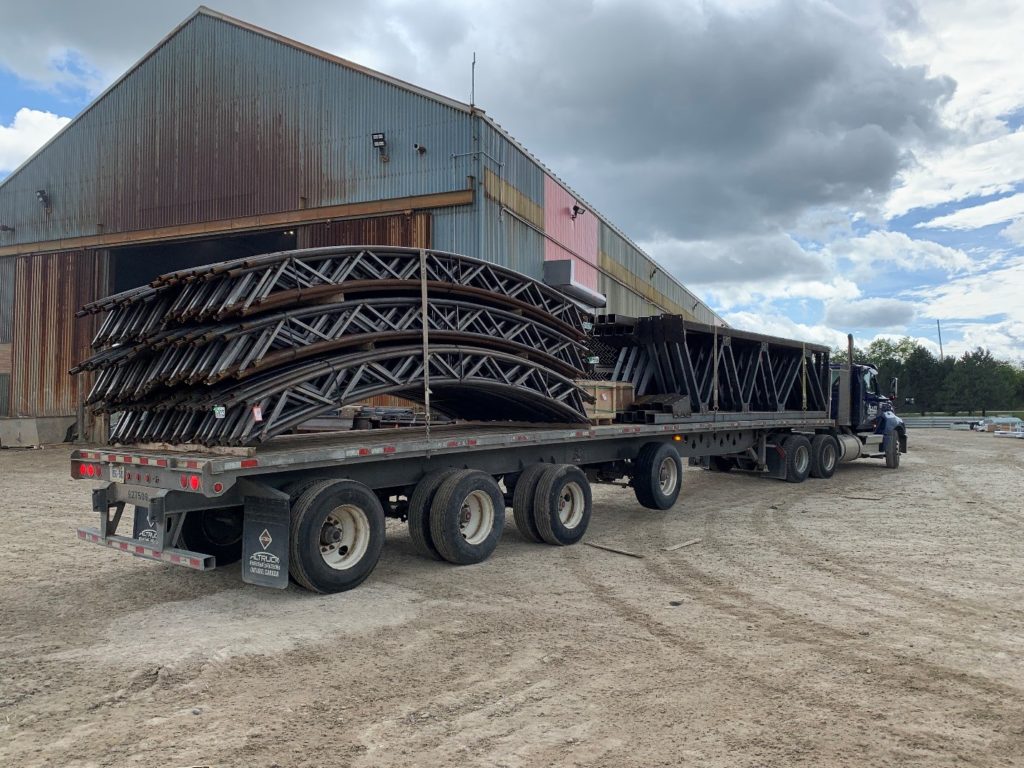
The hot-dip galvanizing process requires the steel to be clean of rust, oil, grease, dust, paint markings, welding slag, and any other debris that may affect the galvanizing process. For this, the steel is inspected and brushed clean as needed before being brought into the facility to start the process (see Figure 5).
After the manual cleaning, the steel is sent through a series of open tanks removing other impurities that can impede the galvanizing process. The tanks contain different solutions for preparing the steel’s surface through caustic cleaning (removal of organic impurities, such as dirt grease and oil), acid pickling (removal of scale and rust), and fluxing (priming the steel to receive the final zinc galvanizing). See Figure 6.
After rinsing the steel in water, it is then primed in a tank of diluted zinc ammonium chloride, which coats the steel, preventing further rust from developing, and primes it for receiving its final zinc coating. Next stop: the galvanizing tank. In this step, the steel is submerged in a bath of almost pure molten zinc heated to 840oF. The zinc metal reacts with the iron on the steel surface to form a zinc-iron alloy coating embedded into the steel surface, making it unremovable — unlike paint. This alloy coating will protect the steel for decades (see Figure 7 and 8).
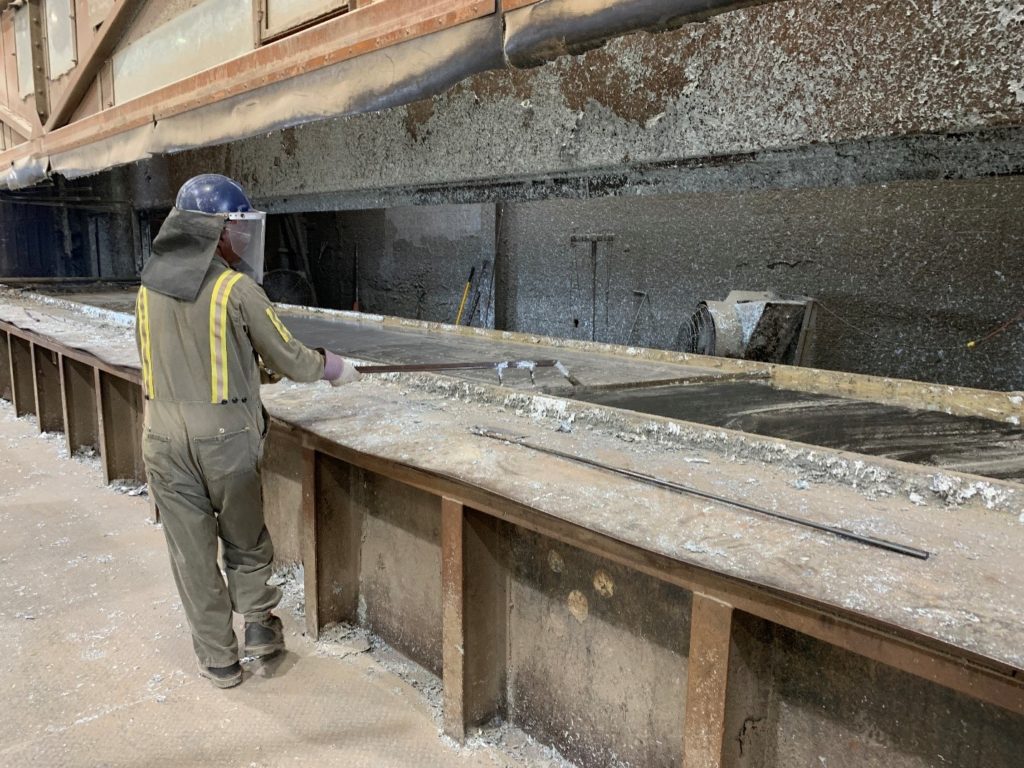
A galvanizing facility goes through a lot of zinc, adding over 5% to the weight of all the steel that gets galvanized. The zinc is delivered in large blocks weighing around 2400 lb. A small percentage of nickel is also added to the mix in the kettle to help stabilize the chemical reaction with the steel fabrications getting galvanized. See Figure 9.
Almost any type of steel product can be galvanized, as long as it can fit in the kettle. See Figures 10 and 11.
The zinc on the outside of the galvanized steel over time reacts with the oxygen and carbon dioxide in the air to form zinc carbonate (which gives it that dull grey colour). Think of zinc carbonate as the steel’s bullet proof vest against corrosion. So, the grey colour is the zinc galvanizing, protecting the black steel from corrosion. It might not last forever, but most of it will outlast you and me!
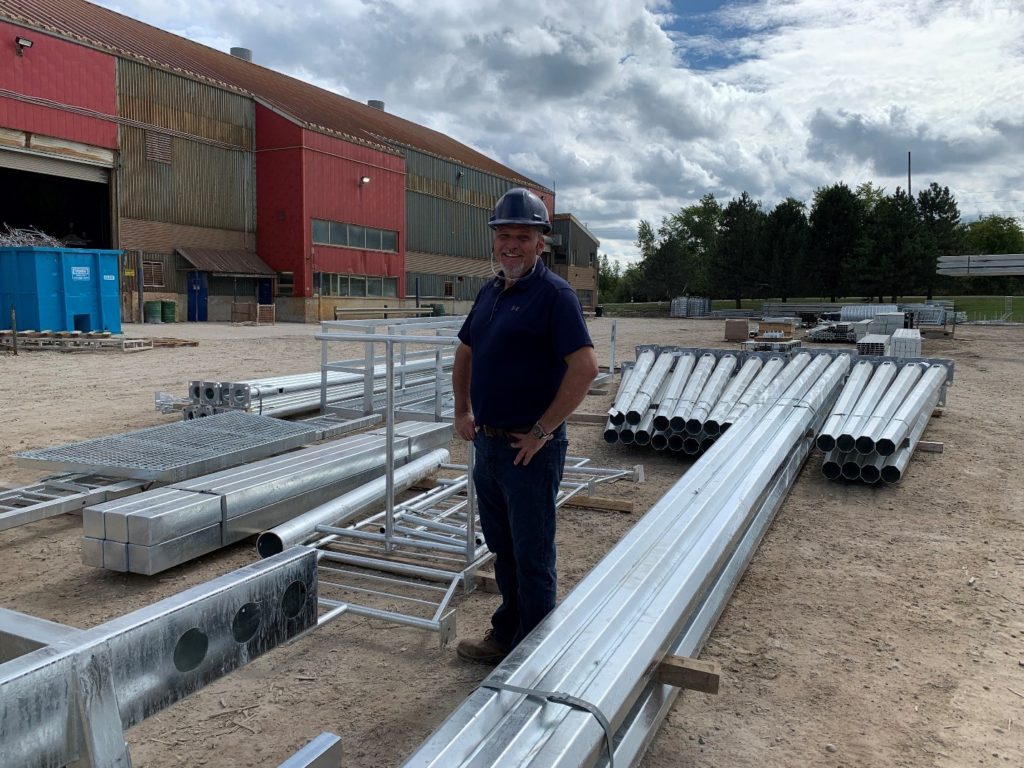
Have you seen an interesting building or piece of infrastructure in or around Southern Ontario that you’d like Eric Chiasson, your personal engineer, to write about?
Send us your suggestions, comments, or questions to articles@local-news.ca and we’ll see what Eric can find out!
Sources:
AZZ Galvanizing website. Url: https://www.azz.com/galvanizing/ (access Sept. 12 , 2022)
Galvanize It: Online Seminar. Url: https://galvanizeit.org/inspection-course/galvanizing-process (accessed Sept. 12, 2022).
For more information on the author: https://www.linkedin.com/in/eric-chiasson-10601082