The definition of a good bridge from a design and construction perspective is a bridge that is durable, low maintenance, and can be built quickly, safely, economically, and with minimal disruption to the public. Although bridges come in all shapes and sizes, over the years several bridge types have prevailed in engineering circles as the most efficient types. Here’s what they are:
A bridge can be divided into two main components. The superstructure is the portion of the bridge up in the air that directly supports the roadway, known as the bridge deck. And the substructure is the portion of the bridge in contact with the ground that supports the superstructure, such as columns, piers, and abutments, as well as their underground foundations (see Figure 1).
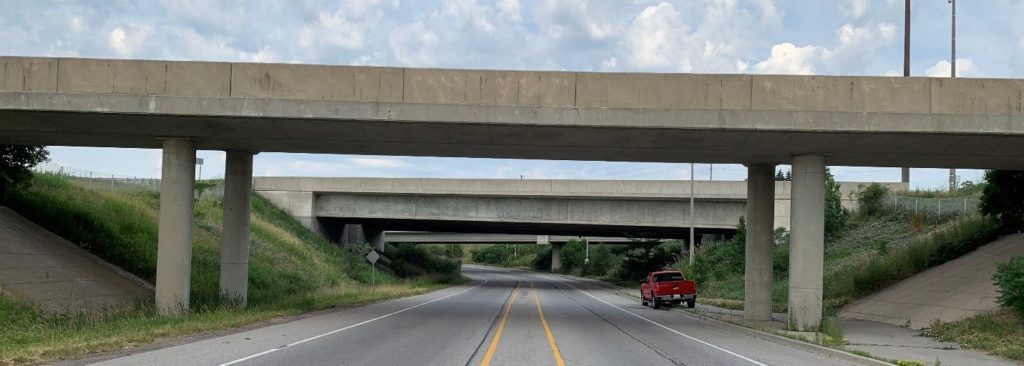
To select the bridge superstructure, the designers need to consider the span of the bridge and the difference in elevation between the two roads (over and under). Different girders and bridge decks have different advantages.
Steel box girders (steel “tub” girders) are typically lighter than concrete and can span longer distances without intermediate supports. All steel bridges built today are made of weathering steel, which is highly corrosion-resistant. It has a special chemical formula (including small amounts of nickel, copper, and chromium) that makes it develop a thin coat of stable adhesive rust that actually protects it from further corrosion. The tub shape (because it’s shaped like a “U”) gives it more stability and a higher capacity than the older style I-beams (see Figures 2 and 3).
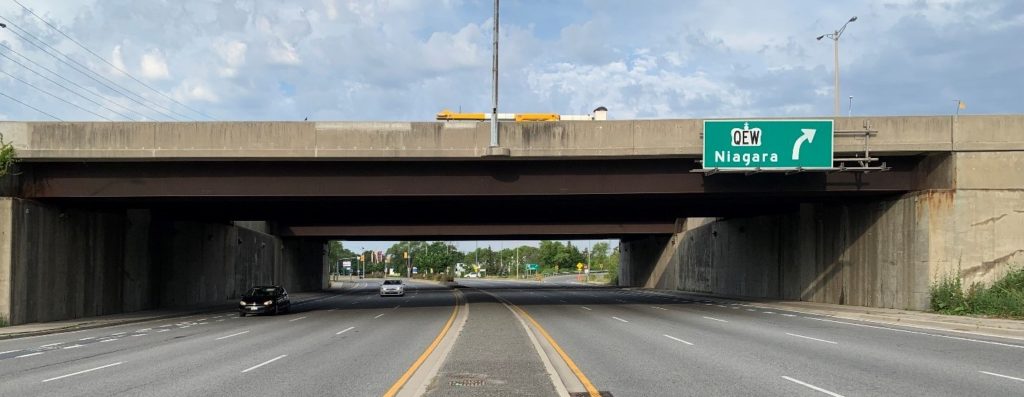
These girders require good welders and require some time to build. Another challenge is that the price of steel is always subject to global market fluctuations unlike concrete, which is mostly made of aggregate, sand, and water — always locally sourced.
Cast-in-place post-tensioned bridge decks are also very common in southern Ontario. As the name suggests, these bridges are completely built in-place using concrete then tensioned using steel cables in embedded conduits in the concrete. This increases the capacity significantly, therefore allowing for longer spans between piers. Another advantage is that they can be much thinner than bridges made of girders, allowing for smaller elevation differences between the bridge and the road below (see Figures 4 and 5). Sometimes the road above cannot be raised high enough for a girder-style bridge.
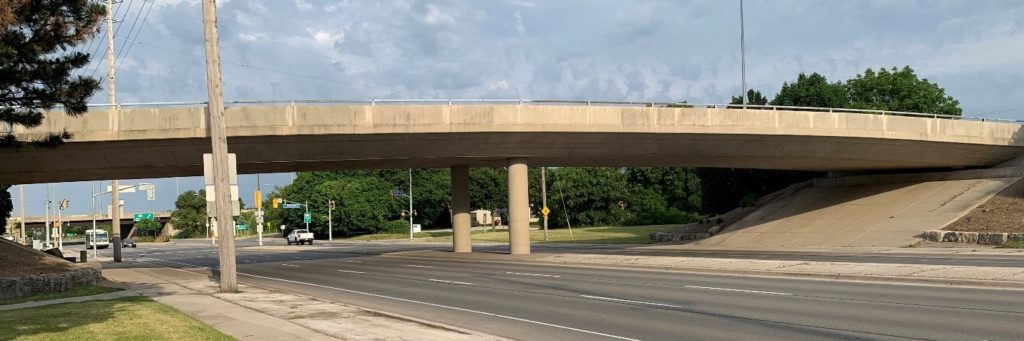
The most common roadway bridge built in North America these days is the precast girder bridge. These girders are much quicker to fabricate than steel girders, and they are made mainly from local materials. Depending on how the precast manufacturer’s facility is set up, girders can be cast two or three at a time in one day! Fabrication is much quicker than their steel counterparts. Their average span is typically less than that of steel girders, but they are very efficient and more cost effective than almost any other type of bridge (for your average local highway type bridge). See Figures 6 and 7.
The longer the span that is being supported by the girders, the deeper the girders need to be to increase their ability to carry all that weight. Of course, the bridge always needs to maintain a minimum clearance to the road below; therefore, increasing the depth of the girders requires raising the road above. Another way to increase capacity of the deck is to instead shorten the spacing between the girders, making room for more. This is a very flexible and efficient design approach.
As you drive throughout the Greater Toronto Area, or anywhere in North America for that matter, most of the bridges you drive over or under will fit one of the descriptions above. Slowly, over time, the most efficient bridge designs prevail, leaving us with the best in technologies and construction methodology… until something better comes along. Take notice and be safe!
Fun facts
The longest precast girders ever manufactured were 205 ft long, installed on the Deerfoot Trail bridge project recently built across the Bow River south of Calgary.
Have you seen an interesting building or piece of infrastructure in or around southern Ontario that you’d like Eric Chiasson, your personal engineer, to write about?
Send us your suggestions, comments, or questions to articles@local-news.ca and we’ll see what Eric can find out!
Sources:
Metal Supermarkets. What is Weathering Steel. Url: https://www.metalsupermarkets.com/what-is-weathering-steel/#:~:text=Weathering%20steel%20is%20a%20family,typical%20low%20carbon%20steel%20grades. (accessed July 5, 2022).
Canadian Precast Concrete CPCI. Record-Breaking Precast Nu Girders Installed in Alberta. Url: https://www.cpci.ca/en/about_us/project_month/april_2002/#:~:text=The%2064%20m%20(210%20ft,if%20not%20in%20the%20world. (accessed July 5, 2022).
For more information on the author: https://www.linkedin.com/in/eric-chiasson-10601082